Why Precision Matters
The Critical Role of Particle Size Distribution in Tablet Dissolution: Why Precision Matters
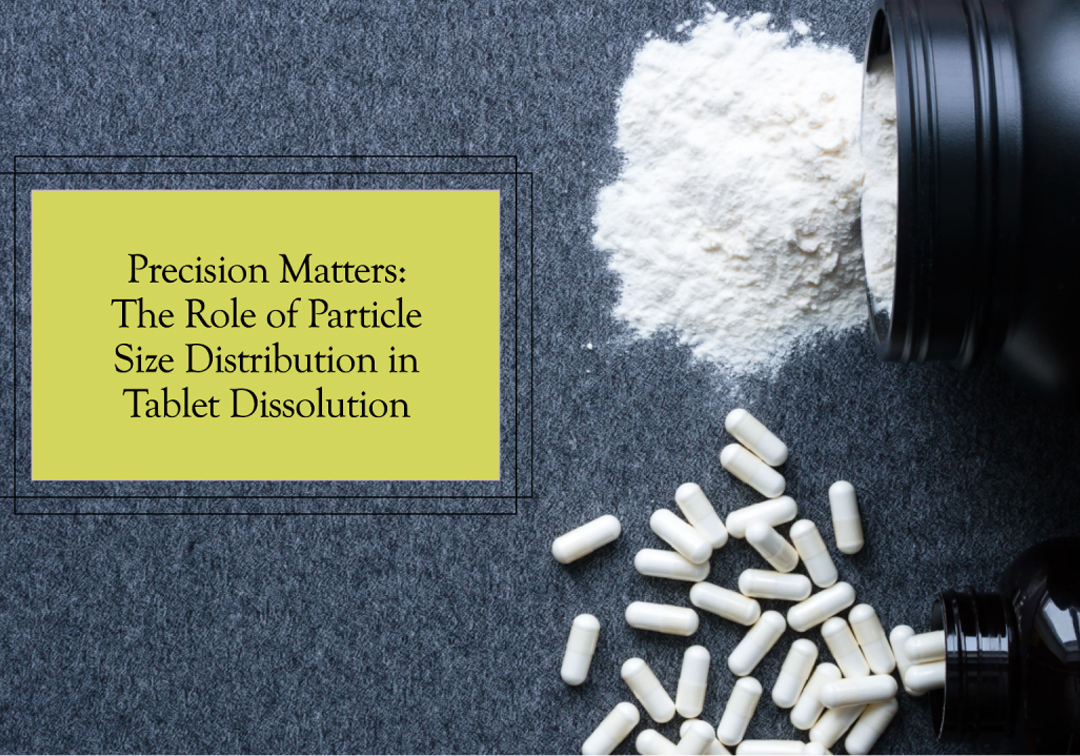
In pharmaceuticals, tablet dissolution is not just a process—it’s a determinant of drug efficacy and patient outcomes. A tablet's ability to dissolve effectively impacts its bioavailability, ensuring that the active pharmaceutical ingredient (API) reaches the bloodstream in the intended concentration and timeframe.
Central to this process is particle size distribution (PSD)—a parameter that often determines the success of a formulation. But what exactly makes PSD so critical? And how can the right equipment elevate the standards of precision and consistency?
Let’s delve into the science of PSD, its impact on dissolution, and how our advanced cone mills are setting new benchmarks for pharmaceutical manufacturing.
Understanding Particle Size Distribution and Its Impact on Dissolution
Particle size distribution refers to the range of particle sizes within a given sample. It’s not just about achieving uniformity but understanding how the size influences key factors like:
Surface Area: Smaller particles have a larger surface area-to-volume ratio, which enhances solubility and promotes faster dissolution.
Solubility and Bioavailability: A controlled PSD ensures the drug is absorbed at the intended rate, minimizing variability in patient responses.
Flowability and Compressibility Uniform particle sizes contribute to efficient tabletting, reducing production issues and ensuring consistent quality.
By optimizing PSD, manufacturers can enhance the stability, efficacy, and manufacturability of the products—making it a cornerstone of pharmaceutical excellence.
AURUS Cone Mills: Precision Redefined
AURUS Cone Mill offers consistency, efficiency, and adaptability and lies at the heart of achieving optimal PSD. Designed with pharmaceutical precision in mind, our cone mills incorporate advanced features to address common challenges faced by formulators and manufacturers.
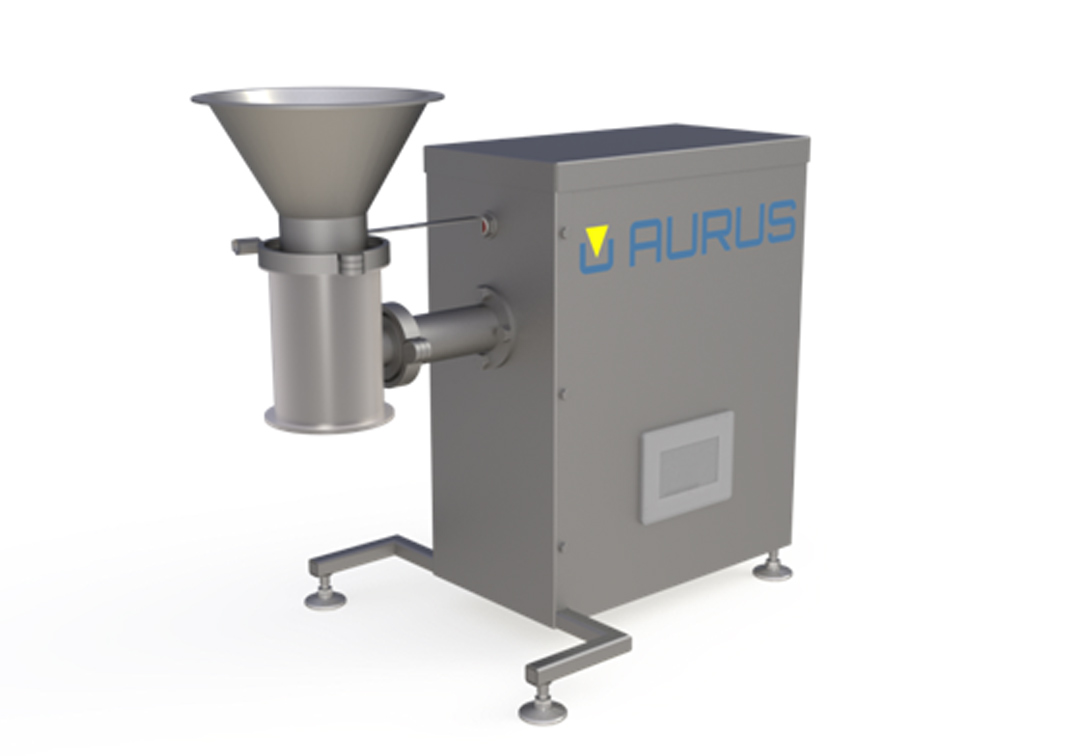
Key Features That Set Us Apart:
Superior Precision: Our mills ensure tight control over PSD, minimizing unwanted fines or oversized particles.
Heat-Sensitive Processing: Built to handle APIs that degrade under heat, our cone mills maintain product integrity without requiring external cooling mediums.
Scalability: Our cone mills offer seamless scalability without compromising performance for R&D or large-scale production batches alike.
Closed-Loop System: Integrated dust-free designs ensure compliance with stringent regulatory standards while protecting operator safety.
Comparative Advantage:
While competitors may offer generic solutions, our cone mills stand out due to:
Innovative Design: Enhanced blade geometry for uniform particle size reduction.
Ease of Maintenance: Modular components allows quick cleaning and minimal downtime.
Proven Results: Real-world case studies have demonstrated up to a 30% improvement in dissolution uniformity when using our equipment.
Real-World Success: A Case Study
A leading pharmaceutical company faced inconsistent dissolution rates during the scale-up of a critical drug. After transitioning to our AURUS Cone Mills, they achieved:
A 25% reduction in batch rejection rates.
Improved tablet dissolution profiles, meeting regulatory requirements seamlessly.
Enhanced production efficiency with minimal downtime.
This success story highlights the transformative power of advanced equipment tailored to industry needs.
Ready to elevate your manufacturing capabilities? Contact us today at sales@kanatengg.com to schedule a consultation, or visit our website to explore our full range of solutions.
Stay ahead of the curve—follow our page for more insights and innovations in pharmaceutical manufacturing.
By prioritizing PSD and investing in superior equipment, you’re not just improving processes you’re safeguarding patient health and setting a new standard for excellence.